Hi, to sign in to your account,
PLACEMAKERS
Opening Hours

Framology - Nog'less Battened Framing
Nog/Dwang free external wall framing with an internal timber batten layer for insulation improves thermal performance.
Nog'less Sheathed Framing
Timber Battens + NZ Standards
Combining an internal timber batten layer for insulation with NZS:3604:2011 clause 8.5.4 (a) Lateral support of studs & clause 8.8.1 (b) Walings
Too often timber wall framing is specified and then constructed in such a way that actually negatively impacts the structure’s overall performance. Sometimes it is a case of ‘less is more’ particularly from a thermal performance perspective.
Nogs/Dwangs have their uses (particularly for some cladding types) but often when not needed for cladding purposes, they still get specified at spacings that contribute to higher construction costs, added weight and, most importantly, compromised insulation performance due to the thermal bridging from un- needed rows of nogs.
What does NZS:3604 say?
NZS:3604:2011, clause 8.5.4 Lateral support of studs
All studs shall be laterally supported by:
Exterior wall cladding complying with E2/AS1 or interior linings complying with section 12. Such material shall be fixed to the studs by direct nailing of cladding or lining material, provided that building paper or similar material not exceeding 3mm thick may separate the lining or cladding material from the stud; or
Clause (a) in a nut shell: if the wall is lined then studs are restrained
NZS:3604:2011, clause 8.8.1 Dwangs & Walings
Dwangs, walings and metal angle walings, where required by 8.5.4 shall be spaced at not more than 1350mm centre to centre and shall be of not less than the following dimensions:
(a) Dwangs: 45mm x 45mm
(b) Walings: 70mm x 19mm
(c) Metal Angle Walings: 22mm x 22mm x 1.2mm
Both sighted clauses endorse the nog'less approach from a NZ Standards perspective.
The BRANZ House Insulation Guide highlights the need to measure and potentially rationalise the percentage of timber in exterior wall framing in an effort to achieve the desired R2.0 construction value directed by H1/VM1 5th edition.
PlaceMakers Frame & Truss is first in market routinely supplying project specific data on the timber to wall area percentage for every build – Framology Timber Percentage Report.
Removing dwangs when not needed and combining the timber framing with an insulated rigid air barrier is one avenue for achieving a true R2.0 construction value in 90mm framing when you are accounting for the presence of all timber within the wall frame.
We are able to supply you with nog-free exterior framing, with a batten layer attached by our Frame & Truss plants in selected regions of NZ.

Secondry Insulation by COMFORTECH®
Comfortech® have developed a Secondary Insulation Layer Wall Solution, which enables the delivery of a 90mm timber frame wall, with a secondary insulation between 45mm thickness internal battens.
This solution delivers a thermal performance which exceeds the thermal performance of a 140mm R4.3 Pink® Batts® by around 20%, while avoiding the supply constraints, additional costs and while also maintaining the bracing performance of the internal lining.
A 90mm frame wall with 30% framing and R2.8 Pink® Batts® Ultra, with a secondary insulation layer of R1.3 between 45mm battens, will achieve a construction R value of R3.3, versus a 140mm wall frame, also at 30% framing which achieves only R2.72. The bracing value of the plasterboard can still be utilised.
More information on the Comfortech® Secondary Insulation Layer Wall Solution can be found here.
![]() |
|
The Framology System
1. Framology Timber Percentage Report
Our Framology Timber Percentage Report; giving you clear, accurate data for calculating H1 compliance
Alignment with the BRANZ House Insulation Guide Tool
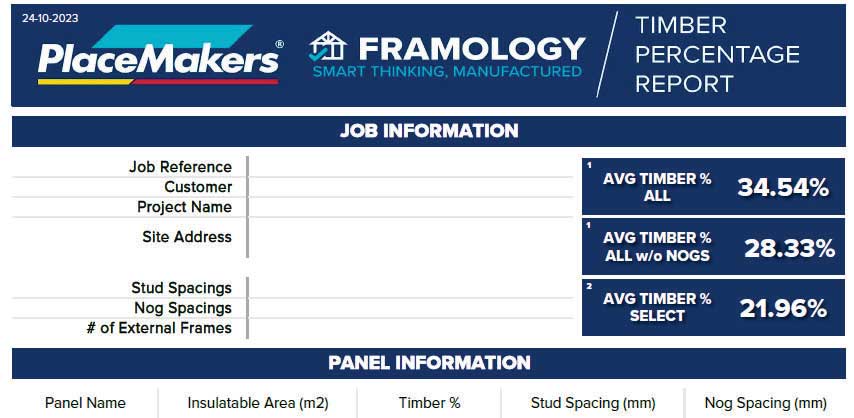
2. Framology Nog’less, Battened Wall Framing
- 70x45 battens factory fixed to interior face of exterior wall framing at 600mm centres to accommodate an R1.3 insulation layer as per Comfortech® solution
- Can be done with 70x35mm battens to accommodate an R1.0 layer
- Removal of nogs and the offsetting of batten timber decreases thermal bridging, improving achieved construction R-value
- Nogging in primary frame can be provided for instances of cladding that relies on them for support and structural cavity battens have not been employed instead
There is a diverse range of cladding products available in the New Zealand market; some rely on the presence of nogs/dwangs for support, others do not. Discuss the compatibility of a nog’less wall system to your project with your lead designer.

TIMBER PERCENTAGE REPORT
Smart thinking, Manufactured.
Discover our Framology Timber Percent Report; giving you clear and accurate data for calculating H1 compliance.
Sustainability
As the industry moves to building homes with improved thermal performance, it is more important for designers and builders to understand what thermal bridges are and how their impact on the build can be reduced.
PlaceMakers Frame & Truss is leading the industry by:
- Providing clear, accurate, project specific data on the timber to wall area percentage (thermal bridging) via our Framology Timber Percentage Report.
- Providing a smart new solution which removes nogs/dwangs, reducing thermal bridging and combining it with internal battens (fixed in factory), for a secondary insulation layer, further boosting R-Value.
![]() |
Building waste is a problem in NZ; we look to partner with recycling companies to ensure that our offcuts don’t all end up in landfill. |